There are many steps in the production process of diamond saw blades, which will be introduced in detail below.
1: Procurement of raw materials: Such as saw blade matrix, bond powder, diamond and other raw materials.
2: Ingredients: The diamond and powder are weighed separately according to the raw material ratio of different formulas.
3: Mixing: Pour all the ingredients into a blender and mix the powder evenly.
4: Granulation or cold pressing: The powder is made into a powder with a granular structure by granulation technology, or the powder is made into a pressed diamond cold-pressed tablet by a tablet machine.
5: Molding: Put the cold-pressed or granulated diamond segment raw material into the mold, and fix the mold.
6: Hot-pressing sintering: Put the mold into the vacuum hot-pressing sintering machine. Generally, Linxing adopts single-mode sintering, which ensures the stability of the segment to the greatest extent. The hot-pressing sintering process includes processes such as temperature increase and pressure increase, heat preservation and pressure preservation, and temperature decrease and pressure reduction.
7: Cooling and demoulding: put the sintered mold at room temperature for cooling, and then remove the cooled segment from the mold.
8: Post-processing: The removed segment needs to be post-processed, such as using a stirring device or sandblasting machine to remove burrs.
9: Welding: mainly through high-frequency welding and laser welding, both the saw blade base and the diamond segment are fixed. High-frequency welding mainly uses high-frequency welding machines, and the process of laser welding mainly requires the use of laser welding machines. After the welding is completed, the tightness of the saw blade segment must be tested, usually by manual clamps.
10: Weld treatment: Whether it is high-frequency welding or laser welding, there will be residual solder or larger welds, which need to be beautified.
11: Saw blade open diamond: The saw blade must be opened before leaving the factory. At present, Linxing adopts the combination of grinding wheel opening and abrasive belt opening to meet the needs of various types of saw blades.
12: Marking or anti-rust treatment: If the saw blade does not need to be printed, then a laser marking machine will be used to mark one side of the substrate. After marking, it is necessary to apply anti-rust liquid to prevent the substrate from rusting rapidly. For customers with higher requirements on the appearance of saw blades, Linxing can also help customers to screen and print the saw blades.
13: Packaging: First use plastic film for inner packaging, and then use carton for outer packaging.
The production process of diamond saw blades is not complicated, but each process has higher requirements for the previous process, one step is wrong, and each steps will be wrong; When producing saw blades, it is necessary to carry out detailed inspections at each step, so that each process can proceed smoothly.

Linsing Diamond Saw Blade Production Process
Publish date:2022-07-04 16:57:47 Article From:Linxing Diamond Tools Clicks:
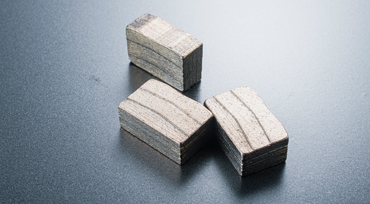
Diamond Segment For Granite Cutting
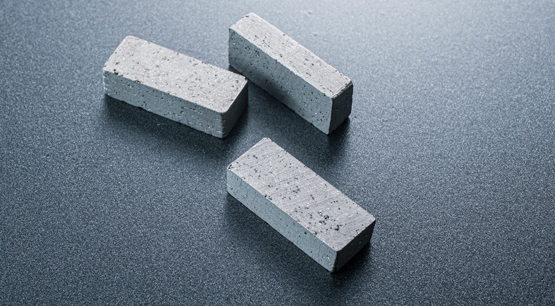
Diamond Segment For Gang Saw
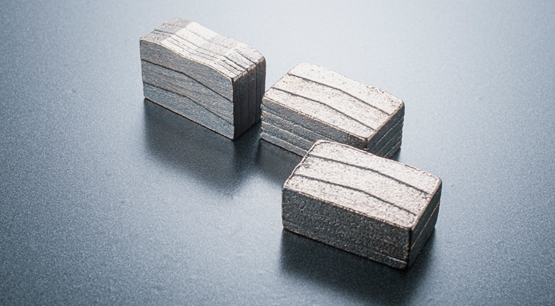
Diamond Segment For Sandstone Cutting
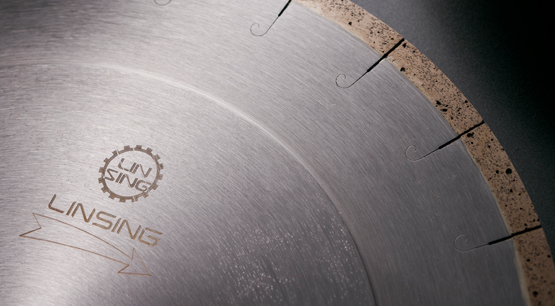
Diamond Horizontal Blade For Marble
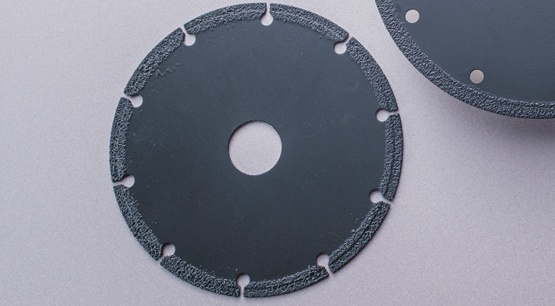
Vacuum Brazed Diamond Saw Blade
Related News
- Liquid phase sintering and solid phase sintering of diamond segment
- HOW TO CHOOSE THE BEST SUITABLE DIAMOND SEGMENTS
- Top 10 Mistakes in the Diamond Segments Selection Process
- Why The Diamond Segments Have Been Processed Into Vavious Shape?
- What should do if the segment is moved grinding during the cutting process?
Related Knowledge
- Attention In The Production Of High-Performance Diamond Saw Blades
- Influence Of Diamond Particle Size On Saw Blade Performance
- Relationship Between Tooth Width Of Diamond Saw Blade And Blank Blade Thickness
- Installation Methods Of Diamond Saw Blade
- Introduction Of Common Parameters Of Diamond Saw Blade

Brazed diamond cutting blade is a very special diamond tool This saw blade uses vacuum brazing to fix the diamond on the saw blade substrate The entire saw blade has a simple structure and less sintering and welding processes, the stability is higher This article mainly introduces the advantages and disadvantages of brazed diamond cutting discs
07/04
2022
Why Are Super Large Diameter Diamond Saw Blades Not Used For Block Cutting?
Diamond saw blades have great application differences according to the change in size For example, the size of the saw blade for cutting blocks is mainly concentrated in 900-3500mm Why aren t super large diameter saw blades used for block cutting? What s the difficulty? Can it be solved? These are the questions to be discussed in this article
07/04
2022