When diamond segments are weld to the circular saw blade, it will often occur one situation that with blisters between the segment and blank blade gap. The specific manifestation is that a lag amount of gas gushes out from the welding seam around the welding seam during the welding of the welding sheet. The gas blows up the liquid solder and flux, and the bubbles will burst to a certain extent. In addition, this situation is boiling, and it will continue for a long time. Only when the molten solder is completely solidified, the "bubbling" site will slowly stop.
After continuous experimentation, it is found that diamond graphitization is the final cause of the blistering of the diamond segments. So why does diamond cause blistering in the welding process of diamond segments?
During the soldering process, especially the high-frequency soldering process, it is necessary to heat the solder tabs and the solder at a high temperature. Once the temperature becomes higher, the diamond powder in the diamond segments will form a large amount of Fe3C with the iron element in the segment. This material is very unstable. As the temperature decreases, iron and graphite are quickly formed. This is called diamond carbonization. Carbonized diamond will release a large amount of carbon monoxide and carbon dioxide gas in the process of reaction. These gases are the continuous gas mentioned in the first paragraph.
So how do we know that diamond will be carbonized? Because diamond will be carbonized at 700-750 degrees Celsius, especially when there is no gas protection, the carbonization temperature will be lower. The welding temperature is greatly affected by the raw material of the welding rod, and the melting point of many silver solder plates is between 650-750 degrees Celsius. If the temperature is not well controlled, the temperature of the segment is too high, and the diamond carbonization will naturally cause bubbling. So why not use other solder tabs with lower temperature? In fact, other solders are not very strong to combine the two. If brazing or soldering is used, the welding strength of the segment cannot be improved very well, so later laser welding methods are gradually introduced to partially replace high-frequency welding.
The poor quality and grade of diamond is also an important factor that affects the welding of the segments. The diamond grade in the segment is poor, the carbonization is more obvious, and the "bubbling" situation will be more serious.
The bubbling of iron-based segment is more widespread. Mainly because the iron element in the iron-based segment can quickly produce Fe3C with diamond, so most of the iron-based segments are currently welded with brazing pads.
As for the solution, first of all, it is necessary to ensure that the welding process is best performed with shielding gas. In this way, the diamond in the segment is guaranteed to have a better quality. Secondly, when grinding the bottom, try not to expose the diamond. The segment only needs to be polished smoother. Then, the welding time is controlled so that the heating time of each segment does not exceed 20 seconds. In fact, if a high-power high-frequency welding machine is used at present, the welding time is three to five seconds, so that the diamond has not been carbonized before the welding has been completed.
All in all, choosing the right solder, higher-power machines, and paying attention to gas protection can completely solve the problem of gas bubbling.

What should We do if the diamond segment is welded with blisters?
Publish date:2022-07-13 16:32:16 Article From:Linsing Diamond Tools Clicks:
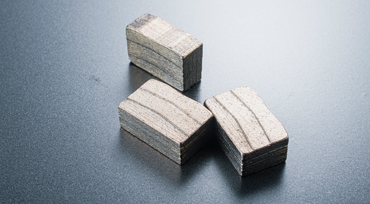
Diamond Segment For Granite Cutting
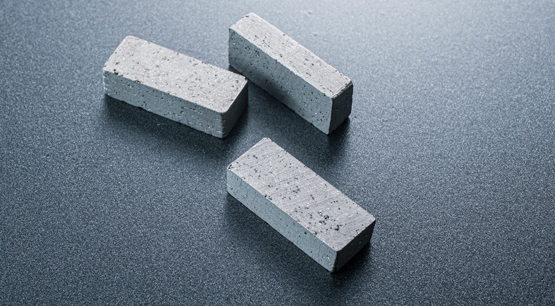
Diamond Segment For Gang Saw
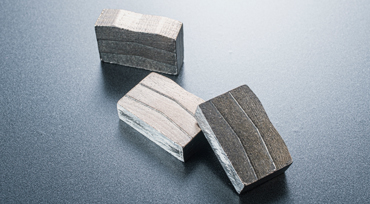
Diamond Segment For Multi-Saw Blade
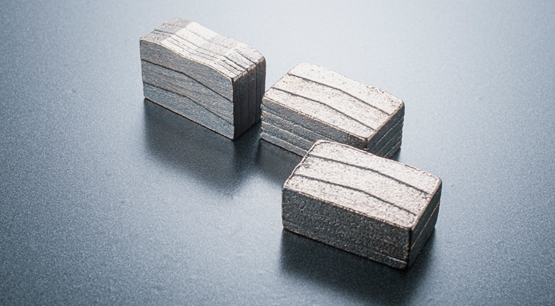
Diamond Segment For Sandstone Cutting
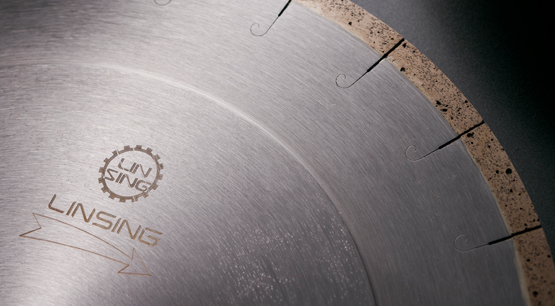
Diamond Horizontal Blade For Marble
Related News
Related Knowledge
- Influence Of Diamond Particle Size On Saw Blade Performance
- Relationship Between Tooth Width Of Diamond Saw Blade And Blank Blade Thickness
- Installation Methods Of Diamond Saw Blade
- Introduction Of Common Parameters Of Diamond Saw Blade
- The Relationship Between Wear Resistance And Efficiency Of Diamond Saw Blades