Diamond segment and base are the two important components of cutting stone saw blades. The stable combination of the two can enable saw blades with any diameter of 105-3500mm to cut stone, asphalt, ceramic tiles, reinforced concrete and other materials with high efficiency and long life. From the perspective of the combination of the two, there are mainly three types of cold press welding, high frequency welding and laser welding. Cold press welding is mainly used for small slices of 105-230mm. This type of saw blade has a short life and mainly through cutting. Does not belong to the mainstream stone processing saw blade, so it is not within the scope of this article.
High-frequency welding, high-frequency welding is to heat the base and segment parts through a high-frequency welding machine, and melt the solder between the base and the segment through high temperature. After the solder is cooled, a stable welding layer is formed. By adding some welding fluxes, the welding layer is tightly combined with the segment and base. The so-called high frequency is only for the speed of heating. Some people call high-frequency welding as brazing (different from vacuum brazing). The advantages of high-frequency welding are as follows. First, because the welding temperature used in the high-frequency welding process is not high, the damage to the base is small, and the base can be used multiple times. Second, with the development of technology in high-frequency welding, the heating speed is getting faster and faster, so a segment can be welded in a very short time, and the welding time cost is very low. Third, high-frequency welding machines are cheap, and almost all segment welding workshops will be equipped, which also reduces processing costs in disguise.
However, the shortcomings of high-frequency welding are also very obvious: First, it can only be used for wet cutting, because the melting point of the silver solder sheet is low. If there is not enough cooling, the segment temperature will rise, which will cause the welding layer to melt and easily cause the segment to fall off or Shift. Second, it is necessary to use solder lugs for welding, and the commonly used silver solder lugs are expensive, and the brazing lugs have insufficient welding strength. Third, although the welding cost is low, the stress tolerance and bending resistance are insufficient, so once the impact force is too large, the torque force will cause the segment to fall off.
Laser welding, laser welding uses a laser method to completely melt the segment and base, thereby directly joining together to form a more stable welding surface. There are three advantages of this method: First, because the welding method is directly used to melt the two, the bonding strength is very high, and there is almost no tooth loss. Second, because the heating temperature is relatively concentrated during laser welding, the advantage of this is that it will not damage the chemical structure of other parts of the segment, and will not have any impact on the quality of the segment and the stability of the diamond. Third, and the most important one, in the case of dry cutting, it can still maintain a good cutting effect, so this type of product is suitable for dry cutting, but also wet cutting. Fourth, such diamond segments will not have oxidation problems, and naturally they will not fall off due to oxidation problems.
However, laser welding also has great shortcomings. For example, first, it can damage the base. Because part of the base needs to be melted, laser welding saw blades are rarely used multiple times. Second, the production cost is high. Laser welding is different from high-frequency welding. It requires a professional laser welding machine and is expensive, so many segment welding workshops are not equipped. Third, although the segment of laser welded saw blades is resistant to high temperature, the base is not resistant to high temperature, so it is often necessary to customize some saw blades with holes.

Advantages and disadvantages of high frequency welding and laser welding diamond segment
Publish date:2022-07-06 18:38:26 Article From:Linsing Diamond Tools Clicks:
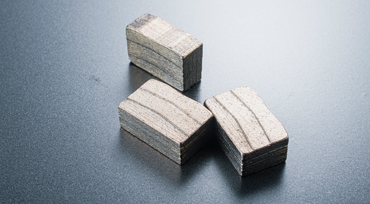
Diamond Segment For Granite Cutting
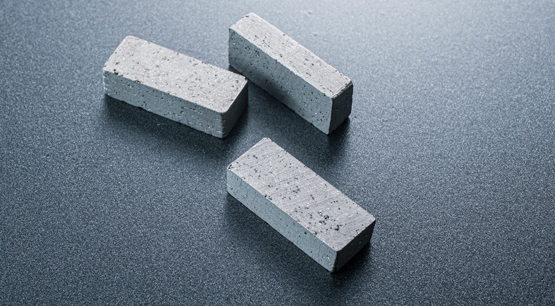
Diamond Segment For Gang Saw
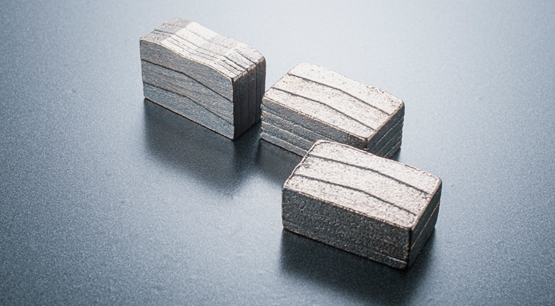
Diamond Segment For Sandstone Cutting
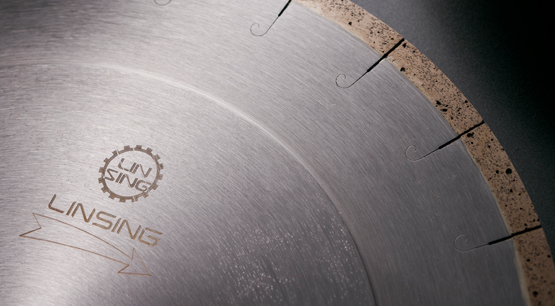
Diamond Horizontal Blade For Marble
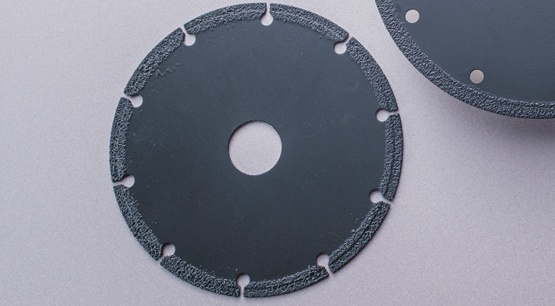
Vacuum Brazed Diamond Saw Blade
Related News
- Liquid phase sintering and solid phase sintering of diamond segment
- HOW TO CHOOSE THE BEST SUITABLE DIAMOND SEGMENTS
- Top 10 Mistakes in the Diamond Segments Selection Process
- Why The Diamond Segments Have Been Processed Into Vavious Shape?
- What should do if the segment is moved grinding during the cutting process?
Related Knowledge
- Influence Of Diamond Particle Size On Saw Blade Performance
- Relationship Between Tooth Width Of Diamond Saw Blade And Blank Blade Thickness
- Installation Methods Of Diamond Saw Blade
- Introduction Of Common Parameters Of Diamond Saw Blade
- The Relationship Between Wear Resistance And Efficiency Of Diamond Saw Blades