The diamond saw blade is welded together by the diamond segment and the saw blade blank. In the actual application process, due to the difference in welding firmness, the saw blade often has the problem of falling off the segment. Why does the blade drop out? How to solve this problem? This is the problem to be discussed and solved in this paper.The diamond segment and the blade blank are weld together in three different ways. In the first type of flame welding, the blade blank and the segment are heated manually through a spray gun, and finally the segment and the saw blade blank can be firmly welded together by completely melting the welding rod. However, this method requires high manual proficiency, and the welding strength is unstable, so it is gradually eliminated by people. The second way is laser welding, which is very strong. But the disadvantage is also very obvious, that is, the blank cannot be reused. The cost of purchasing such a saw blade is prohibitive for blades over D300mm. Therefore, most of the saw blade welding is completed by high-frequency welding. This article also mainly introduces the reasons for the drop of the high frequency welding segment.
1: The solder material determines the firmness of the soldering. There are a lot of welding materials, such as the common copper solder pads, silver copper solder pads, silver solder pads, and phosphor copper solder pads. Due to the stability and firmness of the solder pads, the solder pads with higher silver content, that is, the silver content of the solder pads exceeds 35%, and the performance of such solder pads is the best. During use, the welding strength is the highest and the structure is the most stable.
However, though silver solder tabs are good, they also have disadvantages. For example, the silver solder tab is expensive and the soldering temperature of the silver solder tab is low. In the process of cutting stone, if the temperature of the segment is too high, the segment will still fall out. However, under normal circumstances, the welding strength of silver solder tabs is better than other welding materials, and the silver content is also widely recognized as a standard for the welding firmness of the segment.
2: If the saw blade has a wide range of dropped segments, and the bottom of the dropped segment is relatively smooth, this situation is also extremely common, because the segment is not ground. Since the cutting segment is in the production process, the segment passes through the high temperature and high pressure sintering process. After the internal air is evacuated, the metal on the surface will react with oxygen to produce a layer of oxide on the surface of the metal. This oxide layer can further prevent the tool tip from being oxidized. However, during the soldering process, this layer of oxide layer cannot be combined with the solder, so the segment falls off. Insufficient contact between the bottom of the smooth blade and the welding layer is also one of the reasons for the blade to fall off. Therefore, in order to increase the contact area between the segment and the welding layer and remove the oxide layer, after the segment is produced, the bottom of the segment can be ground with a grinding wheel, so that the welding of the segment is more firm.
3: The power, welding temperature and time of the high-frequency welding machine have not reached the optimum state. Although the purchased solder has a detailed description, in the process of welding the segment, the size of the welding surface is different due to the size of the segment, and the solder can also have different situations. During the process of welding the segment, you should always pay attention to adjustment, high frequency welding machine welding stability= and welding time and other parameters. Through continuous testing, seek the best welding temperature and welding time to ensure the best firmness of the segment. It is best to collect the performance results of various factories and different welding parameters of stone through long-term testing, and finally determine the most suitable parameters.
Of course, the higher the power of the high-frequency welding machine, the faster the welding temperature rises, and the fewer problems there will be in welding. Although a 15kw welding machine can solve most of the welding problems of the diamond segment, if there are higher requirements for welding, it is recommended to use a higher frequency welding machine.4: The strength of welding also includes some human factors. The more skilled operators have a deeper understanding of the welding process, they often determine the strength of welding.

What should we do if the diamond segment is easy to fall off after welding?
Publish date:2022-12-05 13:46:40 Article From:LINSING diamond tools Clicks:
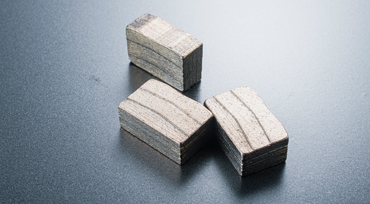
Diamond Segment For Granite Cutting
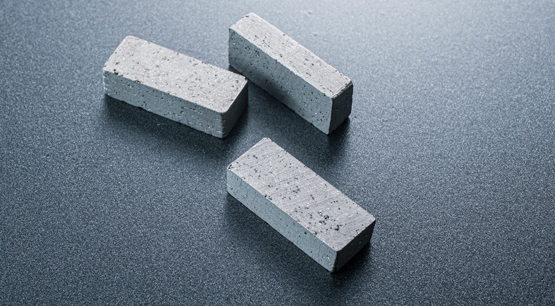
Diamond Segment For Gang Saw
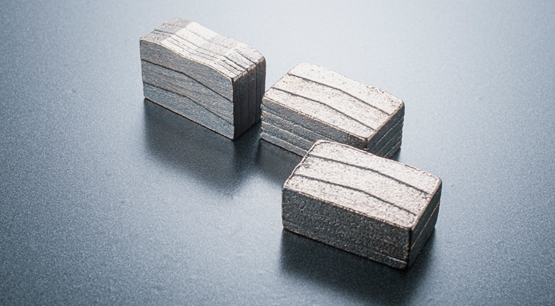
Diamond Segment For Sandstone Cutting
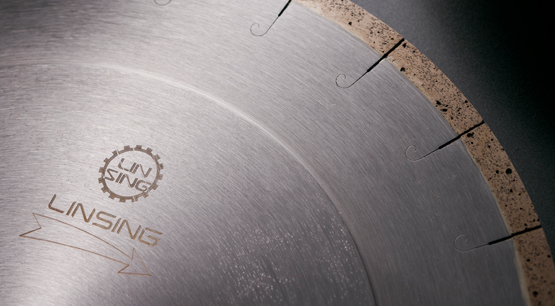
Diamond Horizontal Blade For Marble
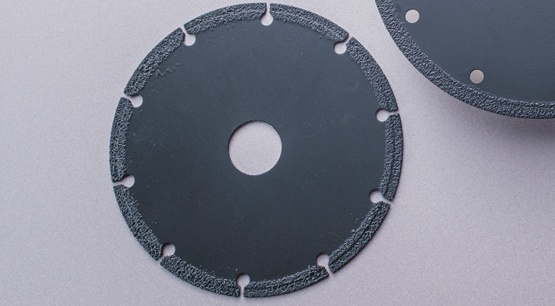
Vacuum Brazed Diamond Saw Blade
Related News
- Several aspects to consider in diamond segment customization
- Diamond segment on diamond requirements
- Liquid phase sintering and solid phase sintering of diamond segment
- 70% diamond segment factory planning adjust price due to diamond powder price is increasing
- HOW TO CHOOSE THE BEST SUITABLE DIAMOND SEGMENTS
Related Knowledge
- Influence Of Diamond Particle Size On Saw Blade Performance
- Relationship Between Tooth Width Of Diamond Saw Blade And Blank Blade Thickness
- Installation Methods Of Diamond Saw Blade
- Introduction Of Common Parameters Of Diamond Saw Blade
- The Relationship Between Wear Resistance And Efficiency Of Diamond Saw Blades