The choice of saw blade segment with diamond needs to be combined with cutting conditions, substrate, segment structure size, tire body, etc. to consider, in general, the harder the stone, the stronger the friction, the faster the cutting speed, the greater the inlet, the greater the impact on the diamond, mainly in the form of impact wear, crushing, shedding consumption, on the other hand, the cut material soft, weak friction, slow cutting speed, small, then diamond mainly in the form of mechanical wear. Hope sawing: diamond in the full play of the premise of moderate impact wear and mechanical wear, and then slightly broken, broken, shedding, so that the blade can play the best cutting role.
Premature consumption or excessive wear resistance of diamonds is not conducive to cutting and processing. The former is diamond does not play a normal role on the fall off or large pieces of debris, premature shedding indicates that the tire body is not dense, not grinding or the diamond holding force is weak, cutting speed or fast inlet, the processed material grinding is too strong, and large pieces of crushing indicates that the diamond quality is poor, low concentration or by too large impact.
Premature consumption results in low blade cutting efficiency and low life, which can be achieved by adjusting diamond quality and concentration and tire resistance. Grinding, using high cut speed, large cut depth, small into the improvement; Light, not easy to produce micro-fragmentation, indicating that the tire body is too wear-resistant or too strong for diamond holding, saw blade cutting depth, small, processed material hard and fine, diamond quality is too good, concentration is too high, diamond particles cut into the rock depth is small, diamond particles affected and cutting force is small, so that the blade is shown as low cutting efficiency, long life. Therefore, it is necessary to adjust the diamond, tire body and the use of low-cut speed, small depth of cut, large inlet to promote diamond micro-fragmentation and speed up tire wear, thereby improving cutting efficiency.
For lower grade diamonds, due to poor resistance to pressure and impact, obvious wear and crushing may occur when cutting general materials, and cutting difficult to process materials will quickly produce large chunks of debris and loss of cutting ability. Therefore, for lower grade diamond, particle size should be fine, concentration should be high, and the tire body should be soft, not too wear-resistant, hot pressure temperature should be low to reduce the impact on diamond, the processed material should be easy to cut materials, so that the role of these diamonds can be more fully played.
For the use of high temperature wear tire body, high grade diamond and cutting difficult to process materials, if mixed with some low grade. Diamond or high-grade diamond quality dispersion, will cause the efficiency of sawing tools, life significantly reduced. In general, the manufacture of large saw blades should be used above MBD6, impact toughness and thermal stability are good diamond MBD6-MBD10 diamond is suitable for soft and easy-to-cut materials such as limestone, medium and hard marble, bluestone; MBD8-SMD25 diamond is suitable for processing hard or medium abrasive materials such as medium hard and above marble, medium hard and below granite and diamond should be coated with surface; MBD10-SMD40 diamond is suitable for cutting hard or hard abrasive materials such as hard granite, sandstone, etc. It is required that the 0magnetic content of diamond should be low, thermal stability and impact resistance should be good, and the surface plated diamond particle size should be used more than 30/35 to 60/70. Coarse diamond is suitable for strong abrasive, hard and brittle, grain v coarse materials, for lower grade diamond, due to pressure resistance, poor impact resistance, in the cutting of ordinary hardness stone may occur obvious wear and crushing, and cutting difficult materials will quickly produce large pieces of debris and loss of cutting capacity. Therefore, for lower diamond, particle size should be fine, concentration should be high, and the tire body should be soft, not too wear-resistant, hot pressure temperature should be low to reduce the impact on diamond, the processed material should be softer stone, so that the role of these diamonds can be more fully played.

Diamond segment on diamond requirements
Publish date:2022-07-07 10:54:21 Article From:Linsing Diamond Tools Clicks:
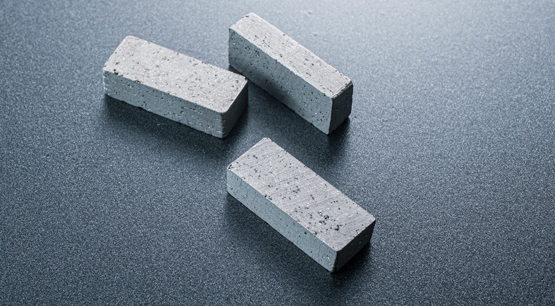
Diamond Segment For Gang Saw
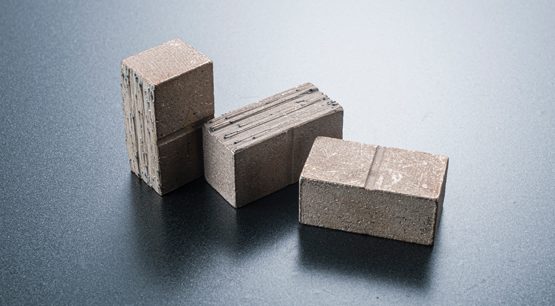
Diamond Segment For Marble Cutting
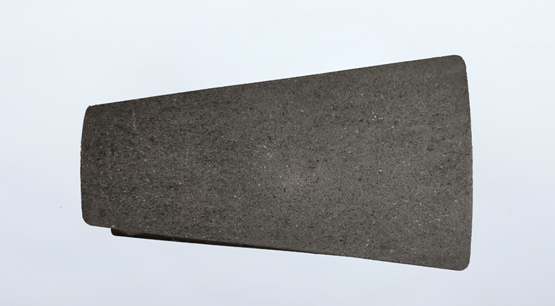
Buff Fickert For Granite
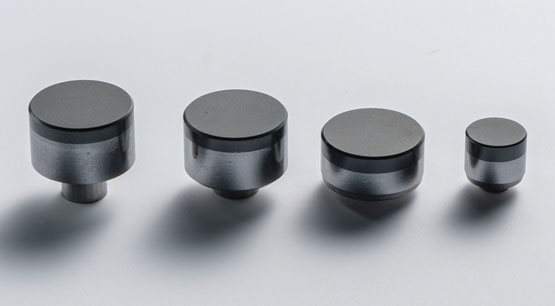
PDC Cutters For Chain Saw
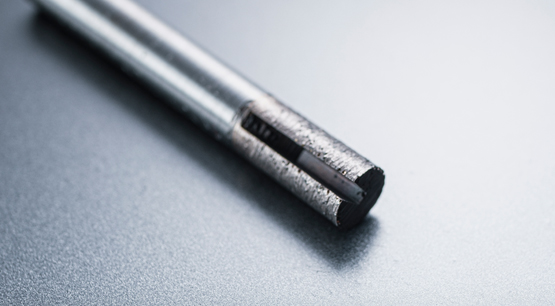
Diamond Sintered Engraving Bit
Related News
- Several aspects to consider in diamond segment customization
- 70% diamond segment factory planning adjust price due to diamond powder price is increasing
- HOW TO CHOOSE THE BEST SUITABLE DIAMOND SEGMENTS
- Top 10 Mistakes in the Diamond Segments Selection Process
- Summary of the shape of diamond segments