The main reasons why the diamond segment should be ground and polished before leaving the factory are as follows:
1. Removal of surface flaws: during the manufacturing process of diamond segments, some surface flaws, such as cracks and pores, will inevitably occur, which will reduce the strength and wear resistance of the segment. Grinding and polishing can remove these surface defects, make the surface of the segment smoother and more uniform, and improve its service life and performance.
2. Improve the surface quality: grinding and polishing the diamond segment can make the surface of the segment smoother and more uniform, and improve its surface quality. This is especially important for some applications that require high surface quality, such as stone processing, electronic component processing and other fields that require high cutting surface quality.
3. Ease of use: the surface of the diamond segment is smooth after grinding and polishing, making it more convenient to use. At the same time, grinding and polishing can also remove some sharp edges and corners, avoiding damage to the workpiece during use and improving the safety of use.
Therefore, grinding and polishing the diamond segment before leaving the factory can improve the performance of the diamond segment and prolong its service life, and it is also one of the important measures to ensure the quality of its products.So how does the diamond segment need to be polished?
At present, Linsing uses sandblasting equipment to carry out the grinding and polishing process of the post-treatment of the segment, which can not only improve the roughness of the segment, but also better bond diamond particles and binders. It can effectively remove dirt, grease, rust and other impurities on the surface of the diamond segment, making the surface of the diamond segment more smooth and uniform, thereby improving the bonding strength and service life of the segment.
The sandblasting process usually includes the following steps:
1. Preparation: prepare the sandblasting machine, sandblasting material and diamond segment.
2. Sandblasting: spray the sandblasting material onto the surface of the diamond segment to make the surface rougher. The time of sandblasting and the type of sandblasting materials can be adjusted according to specific conditions. Generally speaking, colored sand with different colors can make the segment show different colors in the later stage.
3. Cleaning: let the blasted segment go through the segment post-processing machinery, and cooperate with the compressed air spray gun to clean the sandblasting materials and impurities on the surface of the diamond segment to make the surface clean and smooth.
4. Inspection: check whether the surface of the diamond segment meets the requirements. If there is any problem, it needs to be sandblasted again.
5. Drying: place the diamond segment in a ventilated and dry place. After the surface is completely dry, it can be processed or used in the next step.In addition to using machinery, some small segment manufacturers also use manual polishing for fine processing. Generally, grinding wheels are used for light grinding to make the surface of the diamond segment smooth. However, with the changes of the times, this method is gradually being eliminated by mechanical locks.
The grinding and polishing process of the diamond segment can not only make the surface of the segment rougher, but also increase its surface area and flatness, thereby improving the adhesion of coatings or other coatings. In addition, sandblasting can improve the appearance of the segment and make it look more beautiful.

The reason and treatment method of diamond segment needing grinding and polishing
Publish date:2023-04-21 14:15:13 Article From:Linsing diamond tools Clicks:
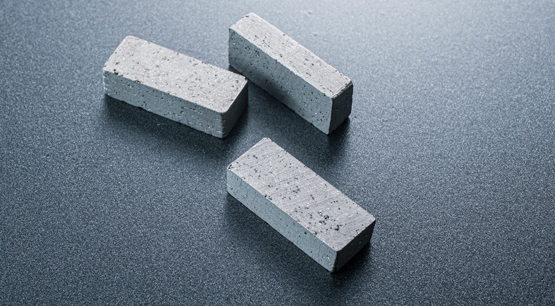
Diamond Segment For Gang Saw
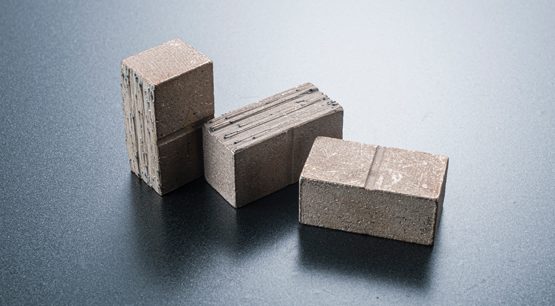
Diamond Segment For Marble Cutting
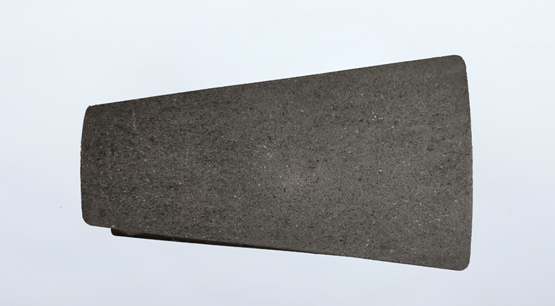
Buff Fickert For Granite

Diamond Core Drill Bit
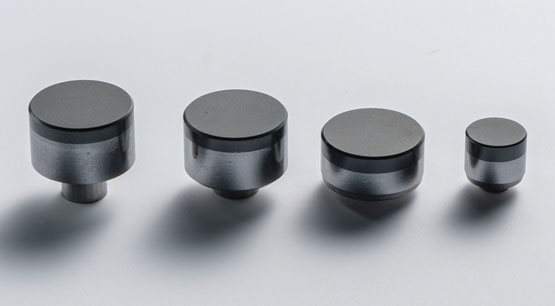
PDC Cutters For Chain Saw
Related News
- Several aspects to consider in diamond segment customization
- Diamond segment on diamond requirements
- Liquid phase sintering and solid phase sintering of diamond segment
- 70% diamond segment factory planning adjust price due to diamond powder price is increasing
- HOW TO CHOOSE THE BEST SUITABLE DIAMOND SEGMENTS